Kinret -Die Casting
Die casting is an efficient, economical process for producing engineered metal under high pressure into molds. The molds are called dies. The dies can make complex shapes with a high degree of accuracy and repeatability. Die cast part can be made to precise dimensions that are both strong and durable.
Advantages of different metal alloy in die casting
- Aluminum is usually Die Cast at 650℃ and can be alloyed with silicon and copper. Aluminum has good corrosion resistance and mechanical characteristic while silicon increases the melt fluidity and copper increases hardness and reduces ductility.
- Zinc is economical for small parts. It is the best alloy to cast and has a lower melting point, 450℃, so the cooling time. Together with the fact that Zinc can be run using a hot chamber process allowing for a fast fill and fast cooling
- Copper has high hardness, high corrosion resistance with the best mechanical properties. Copper alloys are normally used in plumbing, electrical and marine applications where corrosion resistance are important.
- Magnesium is the lightest alloy in common use.
Advantages of die casting
- Compare with sand casting: die casting require little or no machining to meet specifications. It can rapidly produce high volumes of parts without needing to replace the tool and results in excellent surface finish.
- Comparison with investment casting: Investment casting is a high-precision process that employs alloys with properties similar to foundry alloys. Tooling cost is substantially lower than for die casting, but production costs are higher. Investment casting is competitive with die casting only at very low production volumes.
- Comparison with permanent mold castings: Die casting can be made close to dimension specification with thinner wall and holes, can be produced in high rates with less manual labor and less cost per part. Permanent mold casting, however, involves somewhat lower tooling costs and can be made with sand cores yielding shapes not available in die casting.
- Compare with Stamping: If a highly complex stamping or several stampings are required, die casting can be a cost-effective alternative, and can achieve complex shapes which are impossible with stamping. The extra cost for stamping such as fixturing and welding add to the costs of the part, can make die casting very competitive.
What Kinret can do for you?
Kinret die casting services focus on parts for office automation, medical and automotive industries. If you have medium to high volumes of parts from aluminum, zinc, magnesium then it is well worth the investment. Benefits including electro-magnetic shielding, hardness, thin wall thickness construction (minimum 0.5mm).
|
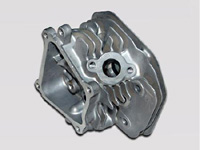
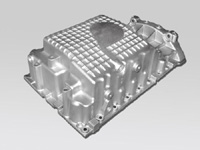
|